Oil Sampling on System Returns
Maintaining the health and efficiency of hydraulic systems hinges on several critical factors, one of which is oil sampling.
Proper oil sampling provides invaluable insights into the condition of your hydraulic oil, enabling proactive maintenance and the prevention of costly equipment failures. There are a few good rules to follow for correctly locating oil sampling ports in circulating systems. It is also important to pay attention to the oil’s Total Acid Number (TAN) and know when to upgrade it through additives or filtration systems as a preventive measure for your hydraulic oil and operation as a whole.
Read more: Store Your Lubricants Right
Locating Your Oil Sampling Port
Sampling ports should be strategically located at points within the hydraulic system where the oil quality can be accurately assessed. This typically means selecting ports at various stages of the system. Here are a few factors to adhere to:
Turbulence
The best sampling locations are highly turbulent areas where the oil is not flowing in a straight line but is turning and rolling in the pipe. Sampling valves located at right angles to the flow path in long straight sections of pipe can result in particle fly-by, which basically leads to a substantial reduction of the particle concentration entering the sample bottle. This can be avoided by locating sampling valves at elbows and sharp bends in the flow line (see Figure 1).

Figure 1. Highly Turbulent Area
Ingression Points
Where possible, sampling ports should be located downstream of the components that wear, and away from areas where particles and moisture ingress. Return lines and drain lines heading back to the tank offer the most representative levels of wear debris and contaminants. Once the fluid reaches the tank, the information becomes diluted.
Filtration
Filters and separators are contaminant removers, therefore they can remove valuable data from the oil sample. Sampling valves should be located upstream of filters, separators, dehydrators, and settling tanks unless the performance of the filter is specifically being evaluated.
Drain Lines
In drain lines where fluids are mixed with air, sampling valves should be located where oil will travel and collect. On horizontal piping, this will be on the underside of the pipe. Sometimes oil traps, like a gooseneck, must be installed to concentrate the oil in the area of the sampling port. Circulating systems with specific return lines or drain lines back to a reservoir are the best choice for sampling valves (see Figure 2).
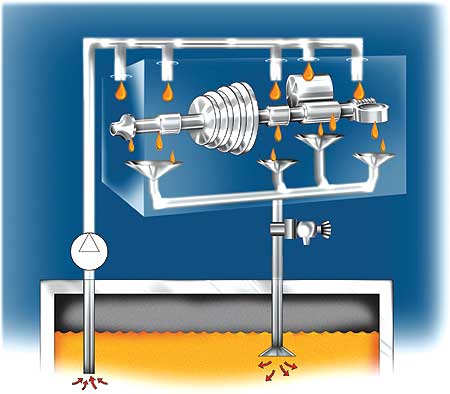
Figure 2. Return or Drain Line
They allow the sample to be taken before the oil returns to the tank and always before it goes through a filter. If the oil is permitted to return to the tank, then the information in the sample becomes diluted, potentially by thousands of gallons of fluid in large lubricating and hydraulic systems.
In addition, debris in the reservoir tends to accumulate over weeks and months and may not accurately represent the current condition of the machine.
The Significance of TAN Upgrades
Total Acid Number (TAN) is a vital parameter in hydraulic oil analysis. It measures the oil's capacity to neutralize acidic byproducts formed during operation. As hydraulic oil ages, it can become acidic due to oxidation and contamination, leading to increased wear and decreased system efficiency. Oil sampling is a proactive measure that can save on maintenance costs and reduce downtime.
Oil Filtration
Oil filtering and recycling play a pivotal role in hydraulic oil systems as they rely on clean and well-maintained oil to function efficiently. Over time, contaminants like dirt, debris, water, and wear particles can accumulate in the hydraulic fluid, degrading its quality and leading to increased friction, component wear, and reduced system performance. Oil filtration acts as the second line of defense (preceded only by a proper storage system) against these contaminants, removing them from the oil and ensuring that it remains free of impurities. In essence, it is another vital preventive measure that preserves the integrity of the hydraulic system and helps to minimize downtime and maintenance costs.
Keller-Heartt has a hydraulic oil filtration service available to regional customers, and you can reach out at any time to connect with someone on the team to learn more.